TRACC-based WCO program boosts OEE and quality at Kenyan tea producer
Finlays is the world’s largest producer of tea extracts and a leading player in instant tea production. The consolidation of two operating units, along with opportunities in product development, left the company with the challenge of integrating the two plants as seamlessly as possible. The development of both people and process capability were critical for a successful outcome to meet customer expectations. Determined to gain competitive advantage, Finlays partnered with CCi to introduce manufacturing best practices through a TRACC-based WCO program.
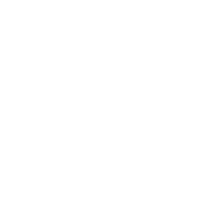
- OEE improved from 42% to 81%
- First pass quality up from 85% to 99%
- Availability jumped from 78% to 93%
- Yield on made tea increased from 25% to 33%
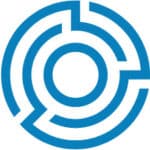
Twenty kilometers from Kericho, in Kenya’s West of Rift Highlands, are some of the world’s largest tea estates. Here, James Finlay Kenya is one of the most prominent tea farms.
Apart from the existing four black tea factories, Finlays had two extract factories that produced instant tea – the manually operated Maramara factory and the automated Soasa plant. In 2010, the Maramara facility was shut down and merged with Soasa.
The integration process presented some challenges, including changes in skill requirements of operational personnel, integration of teams, and technological developments in the
manufacturing lines.
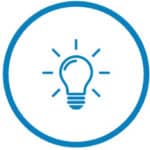
In 2014, Finlays partnered with CCi-GrowthCon to implement World Class Operations. Using the TRACC Value Chain Improvement Solution, plant management was tasked with using OEE to drive performance improvement, including reducing unplanned downtime and improving first-pass quality and yield.
Initial engagement with the workforce was not easy as the business was going through significant transformation, but, by the end of 2015, the organization had fully embraced WCO principles.
TRACC formed the basis of the WCO initiative. Best practices included Leading and Managing Change, Teamwork, Visual Management, 5S, Focused Improvement, Environment, Health and Safety, and later Asset Care. The WCO program was aptly named “Pamoja Twaweza”, which is Swahili for “Together We Can”.
As part of the Focused Improvement Best Practice, the time and material losses were quantified, and Profit Improvement Projects (PIPs) were launched to address the challenges.
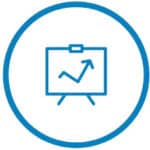
The success of WCO implementation at the Soasa plant has proven that the TRACC Best Practice approach can lead to sustainable performance improvement. This is mainly achieved through building capability within teams, establishing key performance indicators to drive improvements, understanding and solving problems, clarifying roles and responsibilities, implementing standard work, and recognizing and rewarding employees.
A complete culture change has transformed plant performance. Open communication, team meetings to discuss performance, and improved problem-solving capabilities have enabled teams to take full ownership of their respective tasks.
Visible improvements include:
- OEE improved from 42% to 81%
- First pass quality up from 85% to 99%
- Availability jumped from 78% to 93%
- Yield on made tea increased from 25% to 33%
According to Betty Sigei, Continuous Improvement Coordinator, the program has “provided a platform to enable, empower and improve all aspects of the daily operations. Everyone can contribute to serving the customer through improved teamwork and morale.”
Finlays, part of Swire Group, is the leading independent B2B supplier of tea, coffee and botanical solutions to beverage brand owners worldwide. Founded in 1750, Finlays has been sourcing tea since 1817 and producing it since the 1870s. Today, with deep roots across the globe and unparalleled experience and expertise, no one is better placed to unleash the potential of natural beverages by helping brand owners to bring the best from bush to cup. For more information click here.
This resource has been prepared for general guidance on matters of interest only, and does not constitute professional advice. You should not act upon the information contained herein without obtaining specific professional advice. Competitive Capabilities International (CCi) does not accept or assume any liability, responsibility or duty of care for any consequences of you or anyone else acting, or refraining to act, in reliance on the information contained in this resource or for any decision based on it.